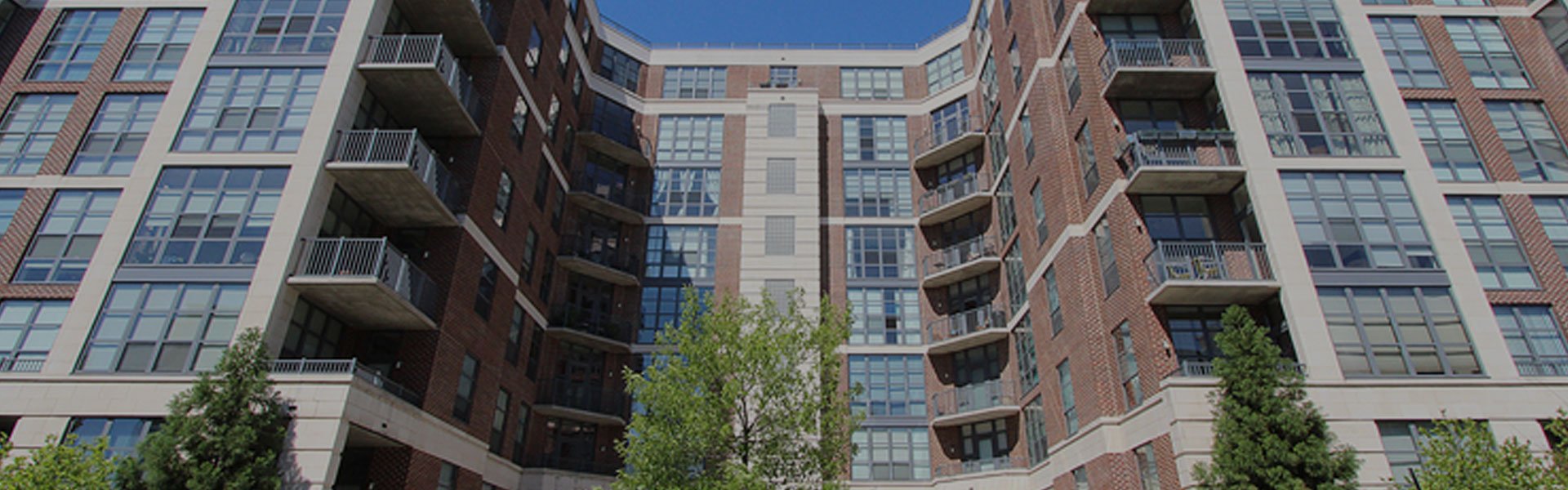
2020 Lofts Condominiums
Washington DC
Project Case Study: 2020 Lofts Condominiums
Building Location: Washington, DC | Building Type(s): Residential Condominium | Project Type: Building Facade Renovation | Total Construction Costs: $830,000+ | Owner: 2020 Lofts Condominium Owners Association
Project Description
The subject building, a 9-story 146-unit condominium building constructed in 2005, experienced water infiltration at the existing aluminum-framed window assemblies. The project was performed in two phases and the scope of work consisted of selective demolition of existing sealants and masonry, installation of through-wall flashing at balcony doors, installation of spray-foam insulation from the exterior at the window perimeter cavities, replacement of window and building joint sealants, selective masonry repair and repointing, masonry and pre-cast cleaning, EIFS restoration and painting and selective replacement of through-wall flashings at balconies and through-wall scuppers.
The work was completed in 2012 through 2015 with a complex schedule consisting of repairs by immediate need for balcony door flashings followed by a tiered mobilization approach for the remaining exterior work. Site conditions presented limited access from the ground due to zero-lot line boundaries, public sidewalks and alleys. Work was performed from aerial swing stage scaffolds. The contractor acquired the appropriate public space permits and erected overhead protection where necessary.
The primary project goals were to prevent future water infiltration at the window perimeters and balcony door thresholds as well as reduce the amount of air leakage the owners were experiencing through the exterior walls. Secondary goals included renovation and repair of facade elements such as building cleaning and EIFS painting to restore the building’s appearance and add select new masonry control joints to prevent future damage to the brick veneer.
Scope of work added during the project included installation of pedestrian coating and restoration of through-wall scuppers and flashings at select balconies, installation of through-wall flashing around penthouse sliding door and window assemblies in the EIFS veneer, painting of all EIFS veneer around the penthouses and inside wall of the parapet wall and restoration of waterproofing below pavers at select balconies.
Process
During the pre-design process, BEC performed several investigations to diagnose and determine causes and sources of water infiltration at the window perimeters and balcony door thresholds. First, BEC performed a destructive investigation at the balcony doors. With the help of a contractor, select masonry was removed to allow observation of construction of the door and wall assembly. Through this investigation, it was determined the masonry veneer through-wall flashing was not properly terminated, allowing water from the wall cavity a direct route of entry to the interior. Next, BEC performed blower door testing at a representative window to observe for air and water infiltration while performed water spray testing as well as selectively demolished interior finishes and construction. Through this investigation, it was determined that the windows had not been properly flashed in accordance with general industry standards. Lack of flashing and location of windows in the wall openings allowed the windows to condensate as well as allowed water from the wall cavity a direct route of entry to the interior. Finally, BEC investigated water infiltration at the sliding doors of the penthouse units on the roof terrace. Destructive examination of the existing EIFS veneer revealed the same lack of flashing termination at the doors as well as failed perimeter sealants which allowed a direct route of entry for water infiltration. Water spray testing of select sliding door assemblies confirmed these findings. Following each investigation, a report with findings and recommendations was presented to the Owner with budget pricing for the recommended repairs.
During the design phase, BEC erected an off-building mock-up wall and window and performed air and water infiltration testing with the recommended repair approach. Testing was performed to validate the recommended repairs and demonstrate the effectiveness of the repairs. BEC prepared a detailed project manual of specifications and project-specific details which were then issued to select bidders. Specifications included masonry repair, installation of through-wall flashing, lintel repair and painting, and EIFS repair. Project specific approaches and details were prepared for each area of work including repair of the window perimeters, repair of the balcony door flashings, repair of the penthouse sliding door EIFS flashing, painting of metal lintels and select window frames and doors, restoration of select balconies including installation of pedestrian coating and scupper repair, and general masonry cleaning. BEC collected bids and prepared a bid summary for presentation to the Owner. BEC advised the Owner of responsible bids and recommended award.
During construction, BEC provided contract administration services and served as liaison between the contractor and Owner. BEC facilitated monthly progress meetings, reviewed project submittals, coordinated sequencing and scheduling, reviewed pay applications and change orders, and provided construction observation during the repairs to verify compliance with the project documents. Construction observation consisted of weekly observations of the work in progress, final inspections of completed work at each tier and maintenance of a project punchlist.
As part of the evaluation phase, BEC performed baseline air infiltration testing utilizing blower door fan equipment at a selected unit where repairs were not completed. Airflow rates in cubic feet per minute were documented through a typical glazing and wall assembly. Once the window and facade repairs at the same unit were completed, BEC performed post-construction testing and again documented the airflow rates in cubic feet per minute. BEC documented that following the specified repairs, there was a 30% reduction in air loss and air infiltration which provided increased thermal efficiency and should have realized reduced heating and cooling costs to the unit Owners.